Rod ends, also known as Heim joints or spherical bearings, are critical components in various mechanical systems, including automotive applications.
Premature failure of rod ends can occur due to several reasons, including:
- Poor Quality Materials: If rod ends are manufactured using low-quality materials or substandard manufacturing processes, they are more prone to premature failure. This can include using inferior grades of steel or insufficient heat treatment processes, leading to reduced durability and strength.
- Lack of Lubrication: Proper lubrication is essential for the smooth operation and longevity of rod ends. Inadequate or improper lubrication can lead to increased friction and wear between the ball and socket, causing premature failure of the joint.
- Contamination: Dust, dirt, moisture, and other contaminants can enter the rod end assembly, causing abrasion, corrosion, and accelerated wear of the bearing surfaces. Contaminants can also interfere with the lubrication, leading to increased friction and potential failure.
- Overloading: Exceeding the load capacity of the rod end can lead to premature failure. Overloading can cause excessive stress on the bearing components, leading to deformation, fatigue, and eventual failure of the joint.
- Misalignment: Improper alignment of the rod end can result in uneven loading and stress on the bearing surfaces. This can cause premature wear and failure of the joint, particularly if misalignment occurs frequently or under high load conditions.
- Impact and Shock Loads: Sudden impacts, shocks, or vibration loads can exceed the design limits of the rod end, leading to stress concentrations, china rod ends manufacturer deformation, and eventual failure of the joint.
- Improper Installation: Incorrect installation techniques, such as over-tightening or insufficient tightening of fasteners, can lead to misalignment or damage to the rod end assembly, resulting in premature failure.
- Environmental Factors: Exposure to harsh environmental conditions, such as extreme temperatures, humidity, salt spray, or chemicals, can accelerate corrosion and degradation of the rod end components, leading to premature failure.
- Fatigue: Continuous cyclic loading or high-frequency oscillation can induce fatigue failure in rod ends, especially if the joint is subjected to repetitive stress beyond its endurance limit.
- Age and Wear: Like any mechanical component, rod ends undergo wear and fatigue over time, especially under demanding operating conditions. Aging and wear can gradually degrade the performance and reliability of the joint, leading to eventual failure if not replaced in a timely manner.
To prevent premature failure of rod ends, it’s essential to use high-quality components, ensure proper lubrication and maintenance, avoid overloading and misalignment, and protect the joints from contamination and harsh environmental conditions. Regular inspection and replacement of worn or damaged rod ends can also help maintain optimal performance and reliability in mechanical systems.
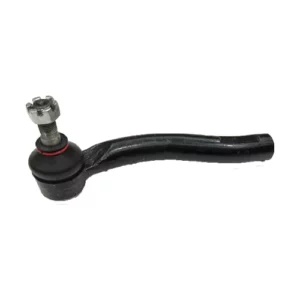